Cycle Counting is an organized division of a warehouse into manageable chunks. Regular counts are required for each “chunk.” These “chunks” can be a range of items and/or warehouse locations. To inspire an optimal use of Cycle Counts, you must employ several strategies. We will explore opportunistic and scheduled counts. We will also go into Blind vs. Shown counts as well as Lost Items vs. Inventory Adjustments. All of these concepts and strategies will help you paint a fuller picture of how to effectively manage and execute your cycle count.
In Cycle Counting: How to effectively use – Item vs. Location, we talked about splitting up your counts by item or by location. In Scheduled & Opportunistic Counting – How to understand the difference, I explained the difference between a Scheduled Count and an Opportunistic Count.
Effective use of Scheduled and Opportunistic Cycle Counts
Effective use of Scheduled and Opportunistic Counting will improve your inventory controls. The utilization of both methods will increase the accuracy of your on-hand reporting. Inventory cost accountants need this to confidently and accurately report these numbers to investors and banking institutions.
As with the approach of locator-based and item-based counting; you must incorporate both styles of counting. This will fully optimize and your coverage and gain full efficiency of your inventory accuracy. The goal here is to use both styles most efficiently. Verification that the system is accurate is an ideal reason to use Scheduled Counting. Fixing discrepancies on the spot is ideal for Opportunistic counts.
Primary Form of Cycle Counts are Scheduled; Use Opportunistic for Spot Checks & Recounts
The ideal warehouse will have 80-90% of its cycle count as scheduled counts. These Scheduled counts will confirm that your physical inventory is in sync with your computerized inventory control system. Opportunistic counts will cover the remaining 10-20% of cycle counts. These counts occur to adjust and realign discrepancies as they occur. Opportunistic counts exist to fix a discrepancy when found.
Additional Strategies to incorporate into your Cycle Counts
After you have devised how you will utilize your scheduled and non-scheduled counts, you will need to define a few more strategies within the count itself. These will aid you in further fleshing out policies and procedures for the types of inventory controls that you want to have in place. These additional areas are as follows:
- Count Visibility
- Count Approvals
- Inventory Adjustments
Count Visibility
Cycle Count quantities are either visible or hidden. The counter will either have a “Shown Count” or a “Blind Count.” Each type has its benefits and constraints. The question on the employment of it will depend on the trust level and sophistication of your workforce.
Shown Cycle Counts
When the counter knows what the target quantity to count is, it is a “Shown Count”. System Counts are a synonym for Shown Counts. In this circumstance, the counter knows what the desired quantity of the item/lot/serial in the location specified should be. This means that the counter is also aware of the physical on-hand quantity not being in sync with the system.
Pro vs. Cons
If the counter is aware of the system quantity on-hand; they may do one of two types of behaviors. The minimalist or the fixated. The minimalist will take a look at the location and may eyeball it and if it’s close enough, they will state that the count is spot on. They may count what is there and do no more.
The fixated will strive to make sure that the count is indeed the count. If the counted quantity is off, they will try to make the count correct. They will look around and try to find misplaced items. This is like asking for a clean workspace; the counter is “tidying” up that location. They are making sure the on-hand information is correct. This may require a little extra effort on the counter’s part to try to figure out why the number is off. For instance, look at a neighboring location. They will strive to meet the number and straighten up and organize while doing it.
This approach will fix other errors as they strive to fix the one issue in front of them. This resolves several issues. However, the time and energy spent on resolving these issues can impact the overall productivity of the warehouse operation. While applauded from a perfectionistic standpoint, order fulfillment is the number one priority of any warehouse.
Inaccuracies could happen with a minimalist counter. A shown count can be a path to a less effective activity. The counter could speculate on if the quantity in the locator is correct and simply enter the shown quantity without actually verifying that it is correct. The counter could also stop counting the quantity on-hand once they reached the shown quantity (in the case of an overcount where the physical quantity is greater than the system quantity).
Blind Cycle Counts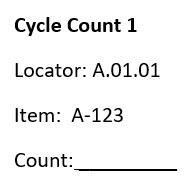
Blind counts are when the warehouse worker is not aware of system on-hand quantity for a given location. Because the ideal number is unknown, the counter must pay attention to the item in question and the quantity in that location. This is designed to drive the worker to honestly and precisely report what they are counting. Therefore, the counter can’t be slacking off and just estimate if the count is correct. They have to know the count.
Pro vs. Cons
If the counter is not aware of the system quantity on-hand; they will count what is in front of them. If Lot number tracking or serial tracking is also in use, they will have to pay attention to those details as well. The positive of this is that the counter has to physically verify the on-hand quantities. The minimalist will not be able to estimate or eyeball a quantity count. Physical accuracy is built into this method. This is because the counter doesn’t know what the system has recorded as on-hand.
The downside of this approach is that you lose out on the proactive alignment opportunities presented by a fixated counter. The counter doesn’t actively know that the count is off. They don’t know to look around to see if an item has been misplaced.
Cycle Count Approvals and Recounts
Any count that is not in alignment with the system quantity will require an adjustment. This will bring both systems into synchronicity. However, how many adjustments will be allowed? If there are a lot of changes, inventory accountants may decide to review them. This may make the process more complicated. Constant adjustments of inventory will cause the daily inventory valuation to not be a solid number for reporting to finance and shareholders.
Auto-approve vs. Recount
All count reviews must meet internal compliance initiatives. ERP systems allow for counts to be automatically approved. This lets the Manager/Inventory adjustment approver only look at and focus on the count variations that are out of tolerance. The review of counts where the physical count is within the tolerance of the system does not need any additional action. If such a review is required, I would recommend a review of your processes and procedures. The reason why I say this is because I have not seen any value in reviewing something that is in compliance. Issues and discrepancies should be the focus.
When requesting a recount, one of two actions can be performed. The same person can perform the recount or a different worker. In some warehouses, I have seen the first count performed by the regular workforce. Shift leads and other supervisors perform the recounts. You do this to confirm that the count is legitimate. If the same person conducts the recount as their first count, there’s a more likely case that the count will not change at all. Either way, the recount process must meet your company’s established policies and procedures.
Inventory Adjustments vs. Lost & Found
There are two main approaches to handling missing material. You can adjust it out of inventory or place it in a pending location until it has been found. The first option is an inventory adjustment. Whereas, the second option is the “Lost and Found” approach. Each one has its merits based on corporate controls.
Cycle Count Inventory Adjustments
Traditional cycle counts are designed to adjust your inventory with each approved count adjustment. This means that if the system thought that there were 20 widgets in locator A and you counted 18, it would issue 2 widgets out of inventory. Conversely, if the system thought you had 20 and you counted 24, it would receive an additional 4 widgets into your inventory on-hand to bring everything into sync. The thought process here is that as you go through the warehouse and count everything, the adjustments would wash out to a zero dollar adjustment.
Several warehouses don’t like this approach. Daily variances and fluctuation of material leaving inventory and then coming back can look suspicious. Auditors usually review and pay close attention to these transactions. High levels of shrinkage are not a good sign. This is an indicator that your inventory controls are inadequate.
Lost and Found
An alternative to the traditional cycle count adjustment is the “Lost and Found” approach. What happens here is that instead of approving an inventory adjustment to “shrink” your inventory, you move the inventory to a designated “Lost” location. This location is not reservable for anything other than an internal warehouse move. The item and quantity are reviewed for increases. They are cross-checked against the lost location. If the material is there; they are transferred to the “found” location from the “Lost” location. Recounts are issued for the adjusted location(s).
For WMS-enabled warehouses, the found transactions are automated upon approval. The system will move the LPN from the “Lost” location to the “Found” one.
This process reduces the number of inventory valuation adjustments. Instead of a daily fluctuation based on cycle counts, there will be a periodic review of lost material. The completed review will dictate what Inventory adjustments will take place. These one-time adjustments are less worrisome compared to a daily fluctuation. However, managing the “Lost” location takes more effort. It is simpler to adjust your on-hand quantities.
Strategy for Cycle Counts – Conclusion
Whether you are scheduling or deciding which strategy to employ to execute it, performing cycle counts are essential to your inventory control structure. There is no one perfect solution for all businesses. You need to examine the pros and cons of each philosophy and decide which will work for your business. Once you’ve employed them, you can begin to reap the benefits.
If you require any assistance with setting up or implementing your cycle counting solution, please contact Perficient and we’ll help you on your way.